The Role of Artificial Intelligence in Streamlining Fulfilment Processes
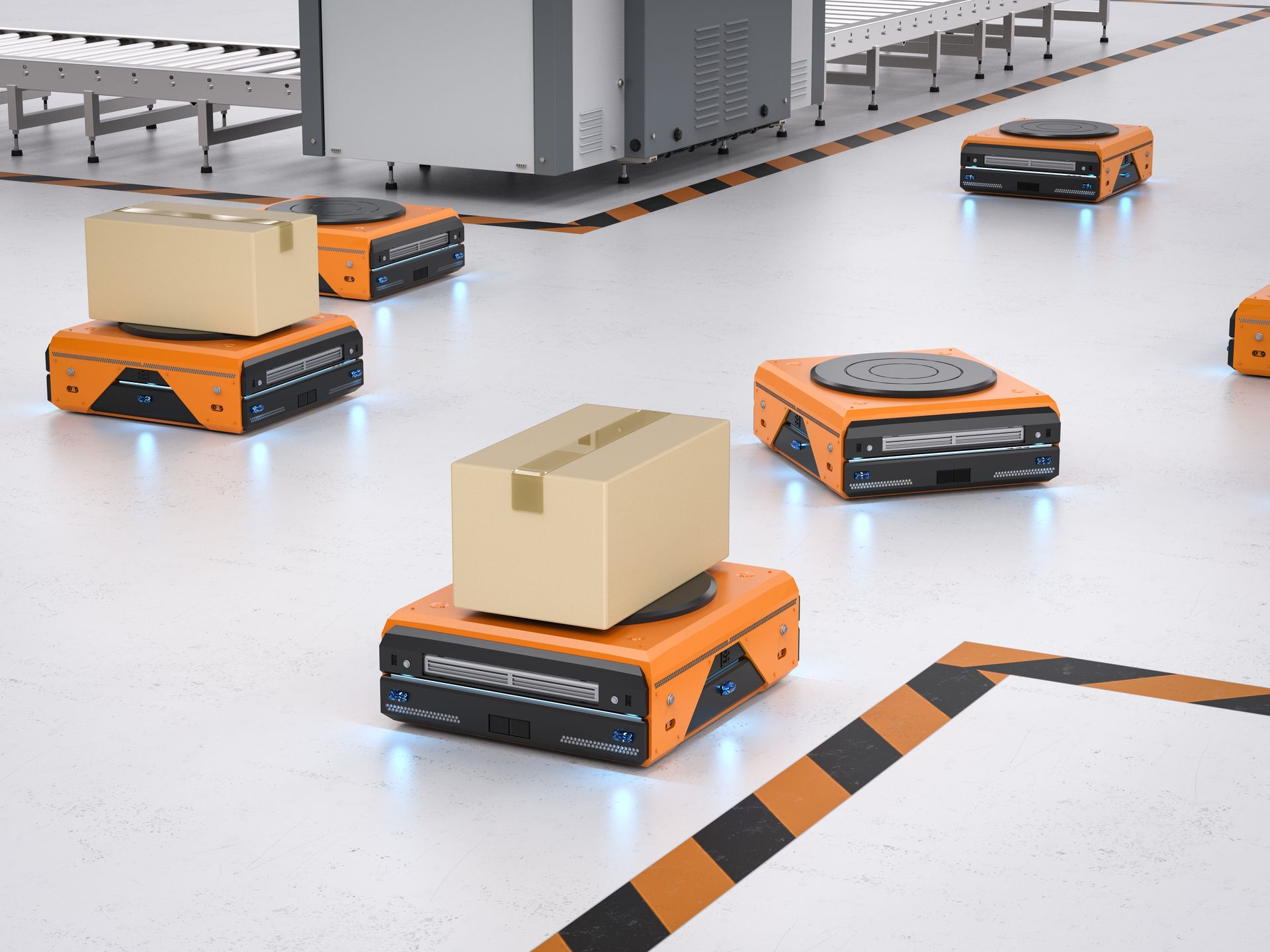
Artificial Intelligence (AI) has infiltrated various sectors of the economy and has proved to be a game-changer in many fields. It is now also marking its territory in the field of warehousing and fulfilment processes, reinventing how companies store, manage, and deliver goods.
The rise of AI in fulfilment processes is no mere trend; it is the future. This blog explores the significant role of AI in enhancing warehouse operations, inventory management, and overall fulfilment efficiency.
AI in Warehouse Operations
Warehouses are the first step in the fulfilment process. As such, operations within these spaces must be optimised for maximum efficiency. AI can help do just that. Here's how:
Automated Sorting: AI-powered robots can significantly speed up the sorting and retrieval process. These machines can work around the clock without tiring, improving productivity and accuracy.
Predictive Maintenance: AI can predict when machinery may fail based on usage patterns. This helps prevent downtime through proactive maintenance, thereby creating a seamless workflow.
Optimised Loading: AI algorithms can plan the most efficient way to load products onto delivery vehicles, considering weight distribution, delivery sequences, and other factors.
AI in Inventory Management
AI, combined with machine-learning algorithms, has the potential to revolutionise inventory management, as follows:
Demand Forecasting: AI can analyse patterns in historical data to accurately predict the demand for individual products. This helps businesses optimize stock levels — enhancing productivity and customer satisfaction while reducing inventory costs.
Stock Replenishment: AI systems regularly monitor stock levels and automatically suggest reorder points. This ensures you never run out of stock while also preventing overstocking.
Monitoring Expired Products: This feature is especially crucial for businesses dealing with perishable goods. AI can track the expiration dates of products, notifying when goods need to be sold or disposed of.
Enhancing Overall Fulfilment Efficiency
The use of AI technology helps boost the overall efficiency of the fulfilment process in several ways:
Improved Order Accuracy: AI systems reduce the risk of human error. This accuracy ensures that customers get precisely what they ordered, reducing returns and increasing customer satisfaction.
Faster Delivery: Through optimised warehouse operations and efficient loading, AI can significantly reduce the time it takes to deliver products. In today's fast-paced world, fast delivery times greatly enhance customer satisfaction.
Reduced Costs: The efficiencies that AI brings can lead to substantial cost savings in the long run. Lower inventory costs, improved warehouse efficiency, and fewer returns can all add up to significant savings.
Given these benefits and efficiencies provided by AI, it’s evident why more fulfilment processes are leaning into AI integration. The interplay of technology in enhancing operations, inventory management, and overall efficiency cannot be undermined. Certainly, the role of AI in streamlining fulfilment processes is bound to become increasingly prevalent in our tech-utilizing world. Interestingly, this is just the beginning — the future of AI in the fulfilment sector holds even more promise. And so, the call to embrace AI is not just about keeping up, but about staying ahead.
Share
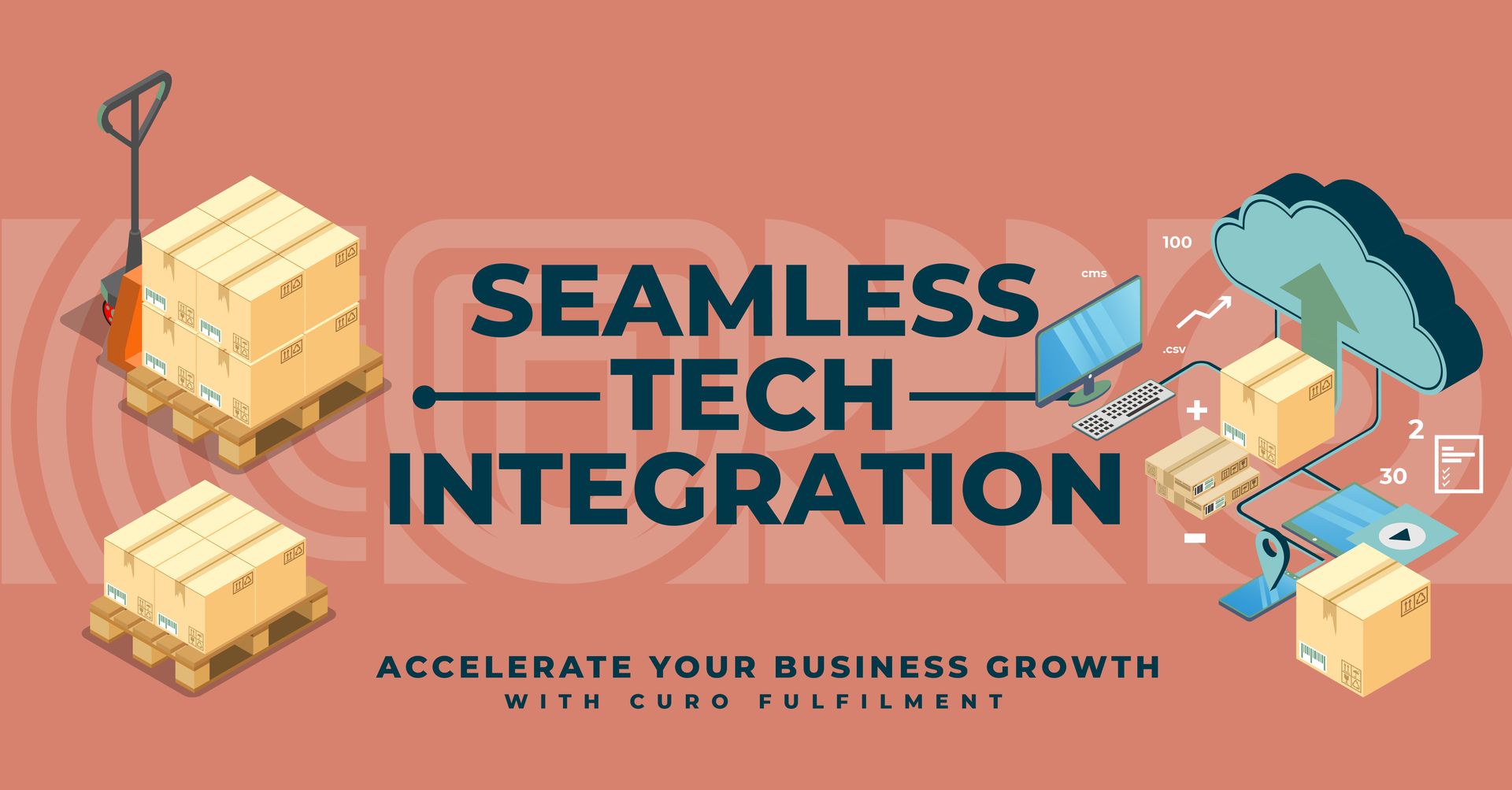
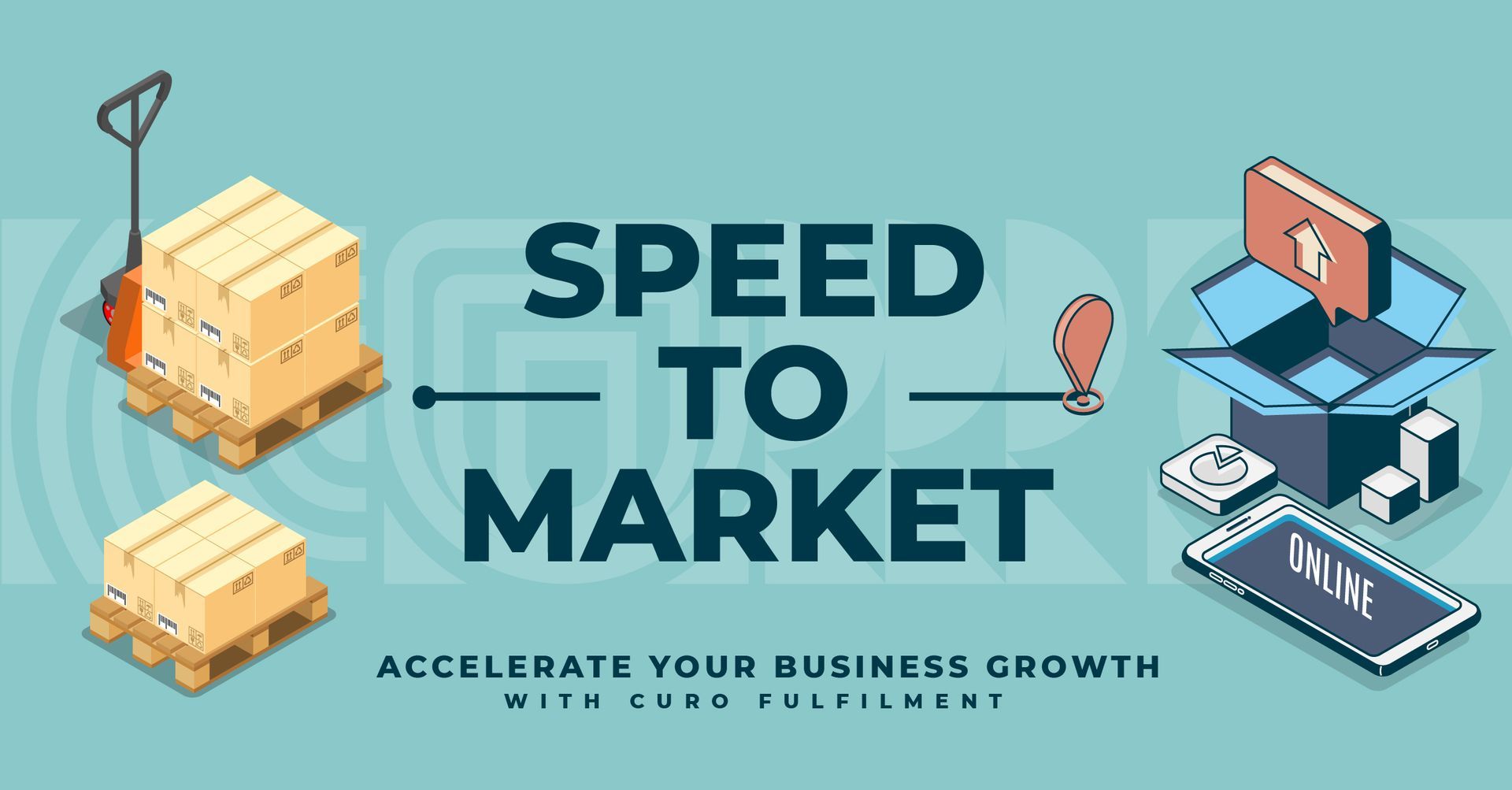
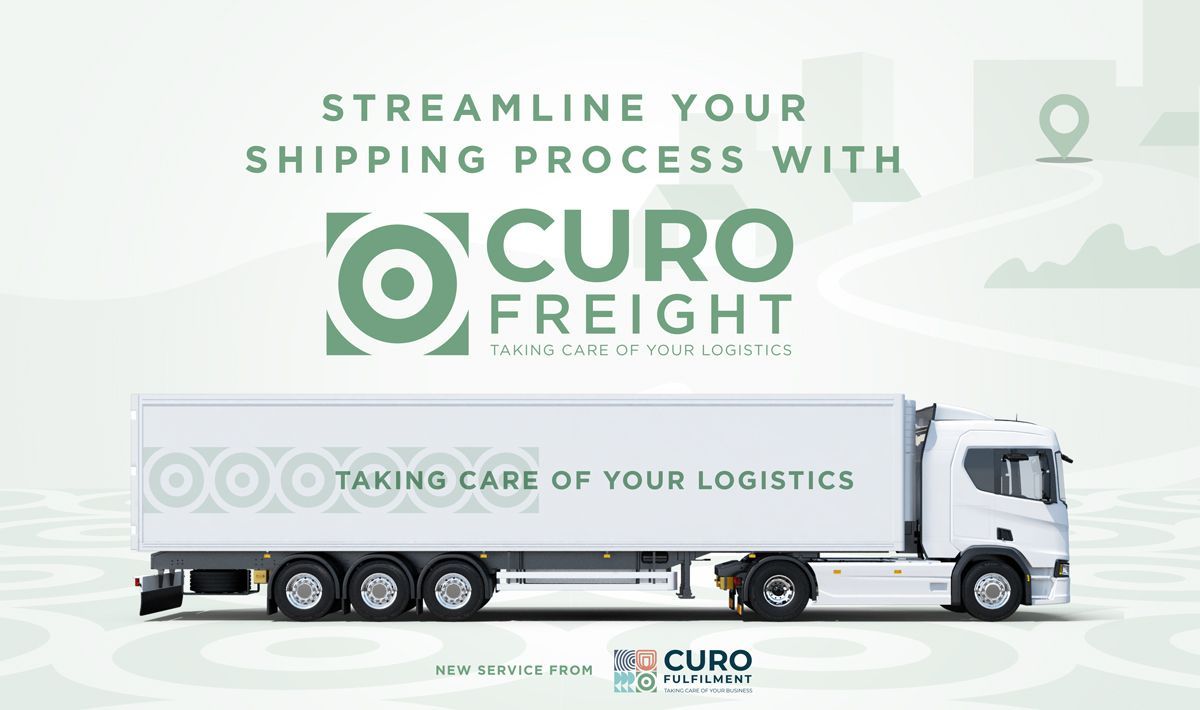
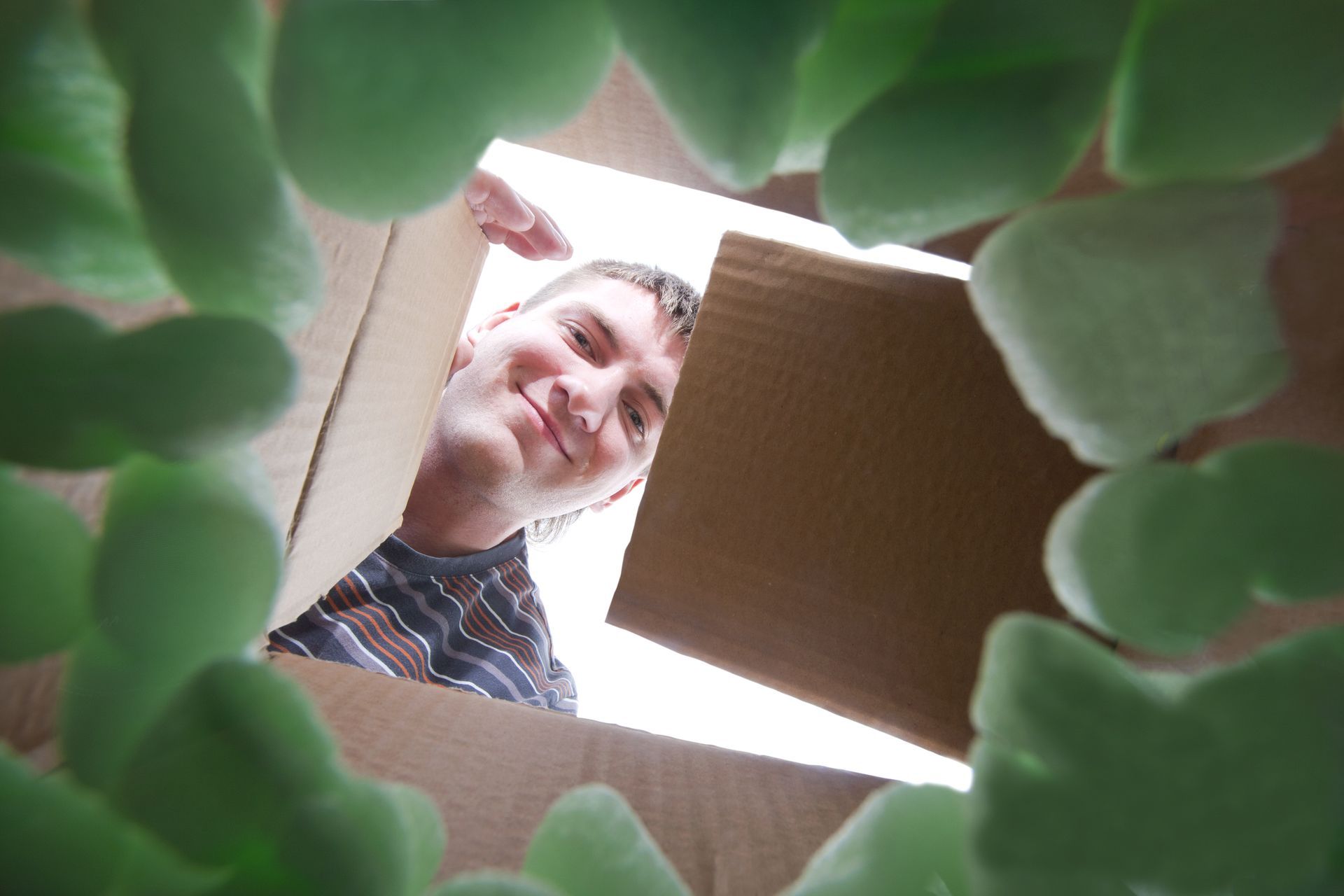
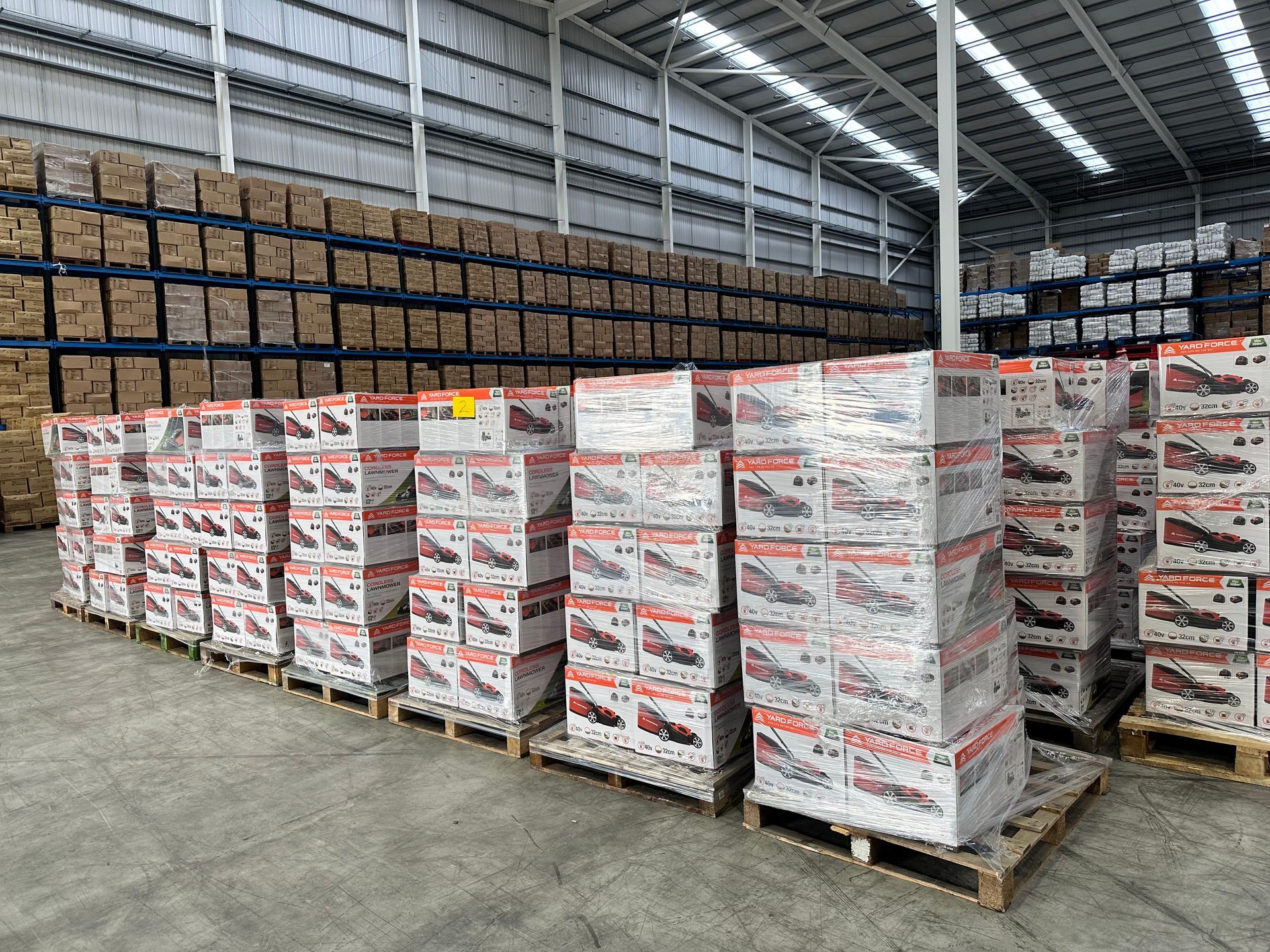
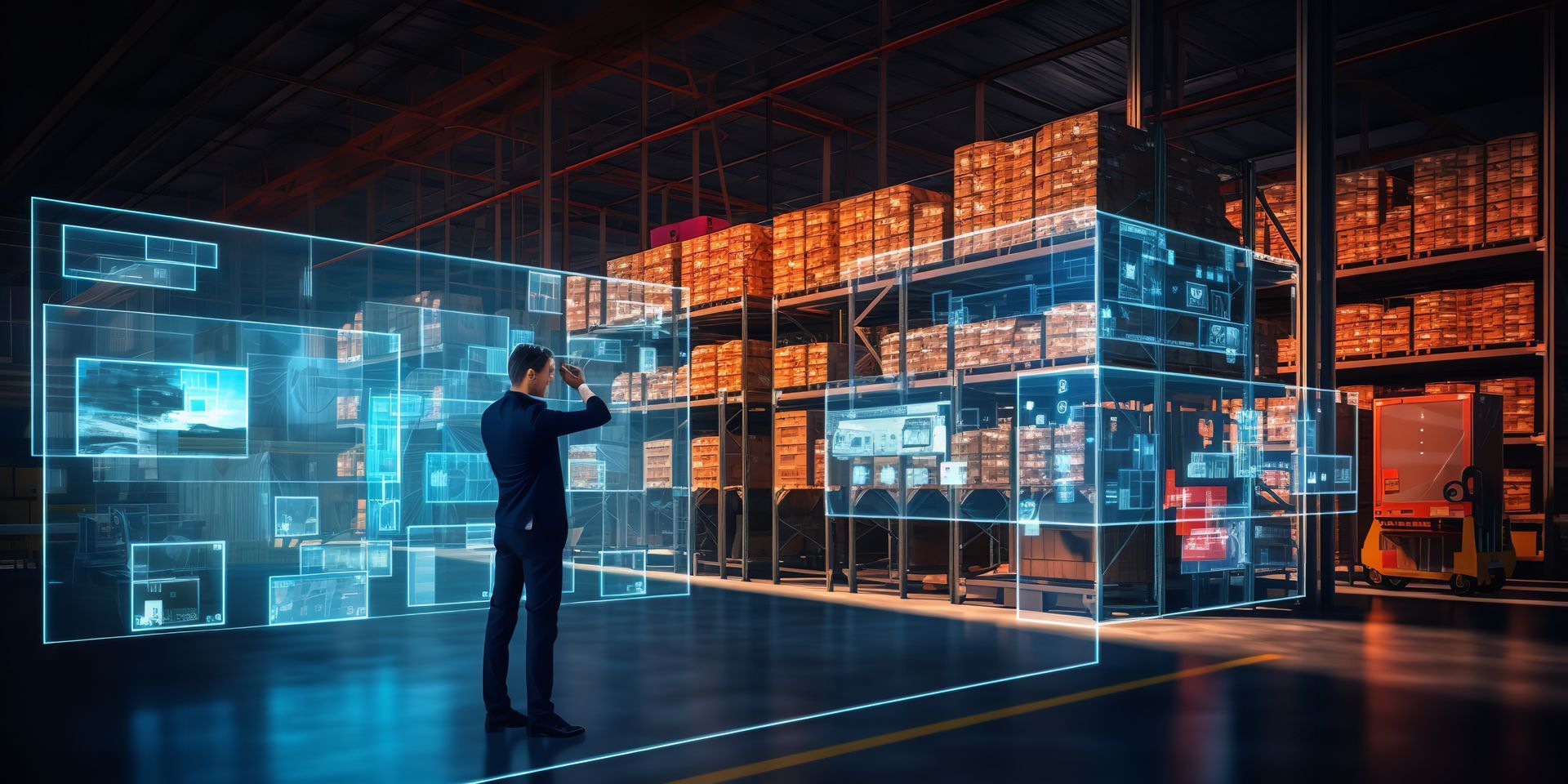
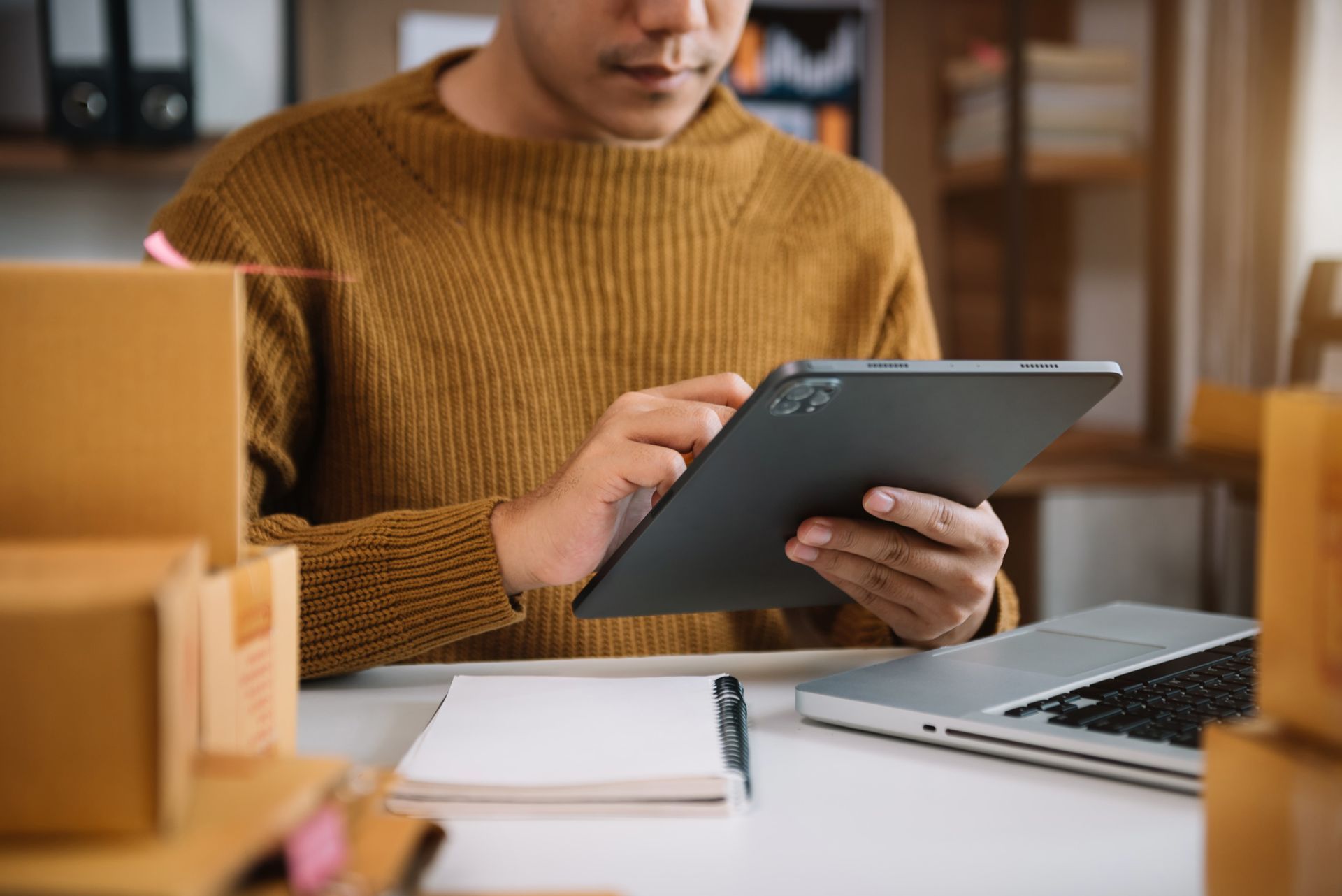

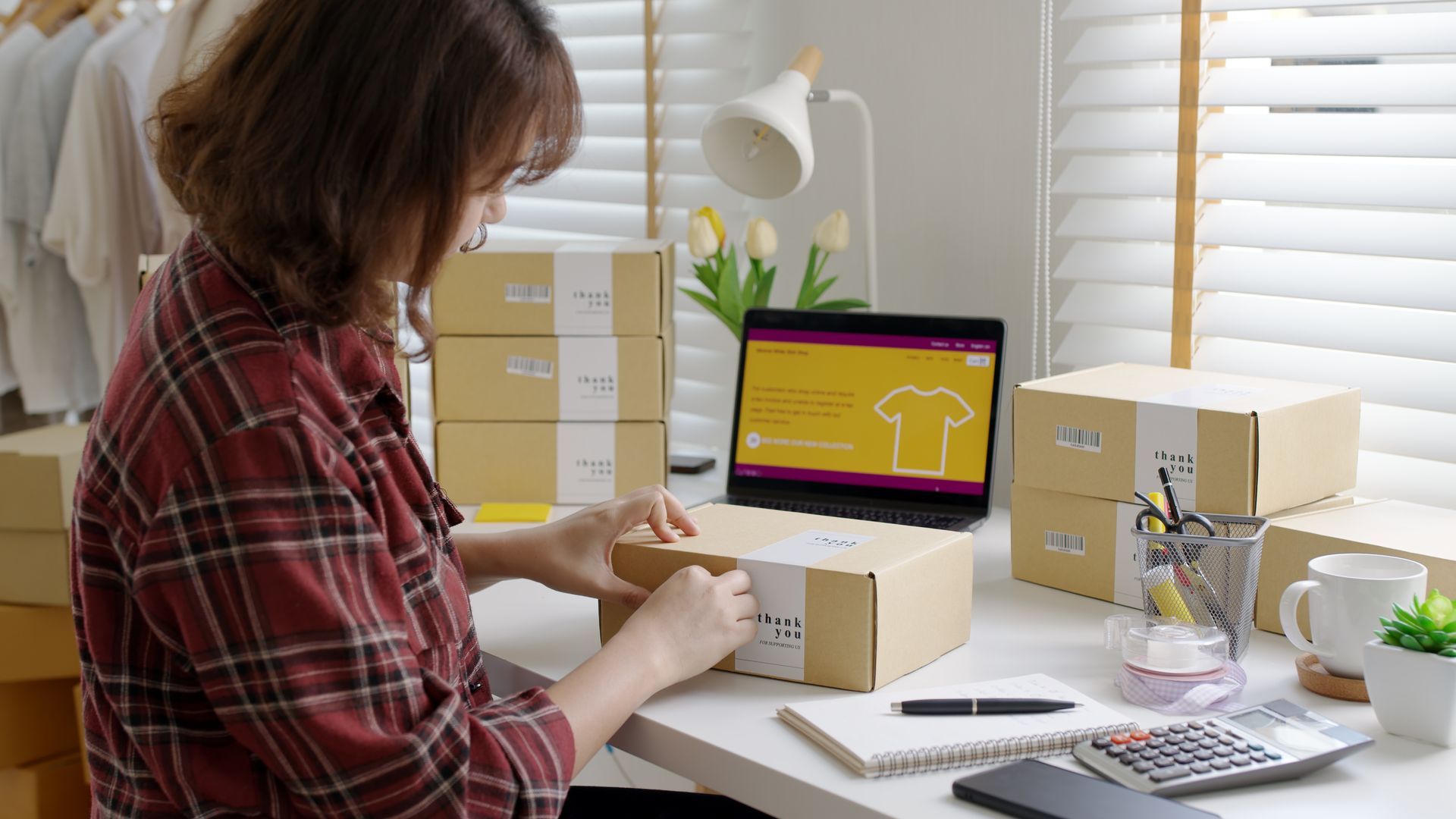